6 Reasons Behind Servo Motor Failure
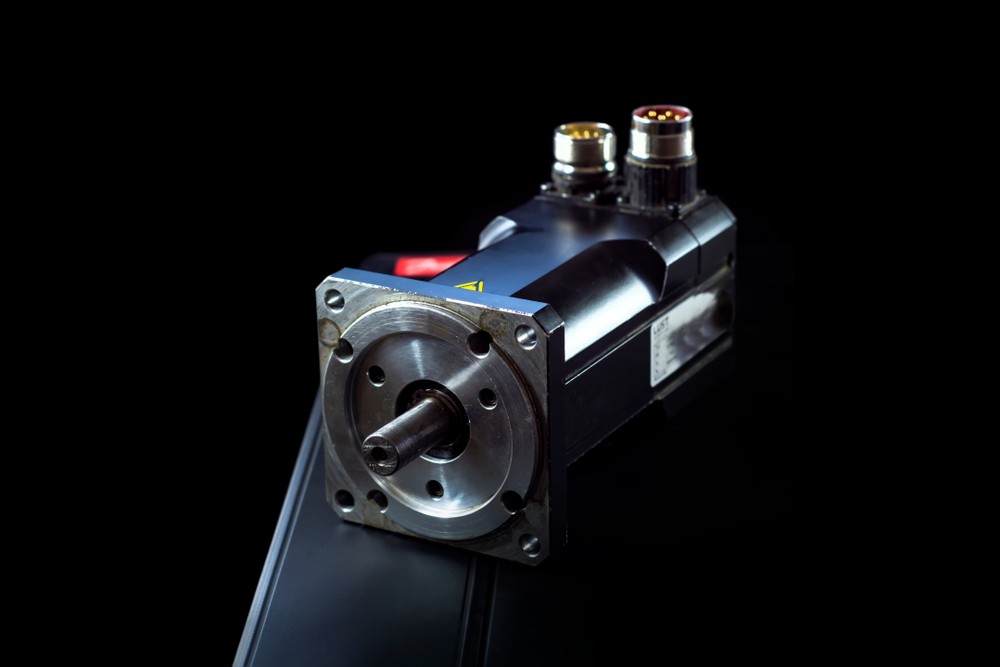
Servo motors are some of the most prevalent components within today’s heavily roboticized facilities. They’re instrumental in the operation of sophisticated machinery and precision tools — everything from assembly robots to multi-axis milling equipment. Naturally, if these components fail, so does the functionality of whatever equipment they’re powering. Unfortunately, servo motors do fail on occasion, for any of several reasons.
Servo motor basics
Servo motors are essential components that wield and exert considerable power. Featuring a positioning device that provides useful feedback and extra control, servo motors deliver power to a variety of machinery and equipment on the factory floor — including next-gen technology like robotics or anything with an automated process.
Virtually every industry relies on servo motors to power equipment and essential to day-to-day activities. Even one faulty or damaged motor can bring production on the factory floor to an immediate halt. There’s a constant need to ensure the functionality and integrity of servo motors, and it starts with proper maintenance.
Common causes of servo motor failure
While there are signs that can indicate a failing servo motor, there’s no substitute for regular inspections to ensure functionality. Routinely assessing the integrity of servo motors is the easiest way to spot common catalysts that cause failure. Some of the variables to observe and remediate include:
- Excessive heat and overheating. Overheating is often the result of an overcurrent on the machine caused by mechanical problems like brake issues or failed mechanical binding. Regulate the temperature of servo motors by replacing worn components, using fans, and giving the motor occasional breaks to promote proper cooldown.
- Dust and contamination. Factories are inherently dirty, so it’s no surprise that contamination from dust, oil, and more can make its way into servo motors and affect everything from bearings to brakes. A dirty servo motor must be disassembled, cleaned, and reassembled.
- Bearing-related failures. Bearing-related problems are easy to spot by the high-pitched, whining noise they produce. Whether it’s an unlubricated bearing or a worn-out one, changing the settings of the servo motor can resolve the issue. If that doesn’t work, you’ll likely need to replace the bearing.
- Electrical faults and failures. While servo motors operate mechanical equipment, problems can still occur to any of its electrical parts. That means checking for any issues with the drive, positioning controller, or other electrical components to ensure they’re operating as expected.
- Mechanical faults and failures. Mechanical issues lead to servo motor failure. From circuits to drive gears, mechanical components can wear down over time, disrupting the ability of a servo motor to adequately power equipment. Maintenance failures often play a role in mechanical faults.
- Maintenance neglect. Servo motors need regular attention, and neglected motors can fail at any time. Bearings may wear out, fluids may build up over time, and plenty of other problems can arise without proper attention. Scheduling regular maintenance helps avoid complete failure and the costly repairs that accompany it.
The value of expert diagnosis and care
Not every servo motor involves the same variables, which makes the expert eye of a maintenance professional prudent in diagnosing and treating issues. By investing in routine maintenance and developing a strong partnership with a trusted maintenance provider, it’s possible to avoid the high costs of servo-induced downtime and keep production on track.