5 Ways to Extend Electric Motor Life
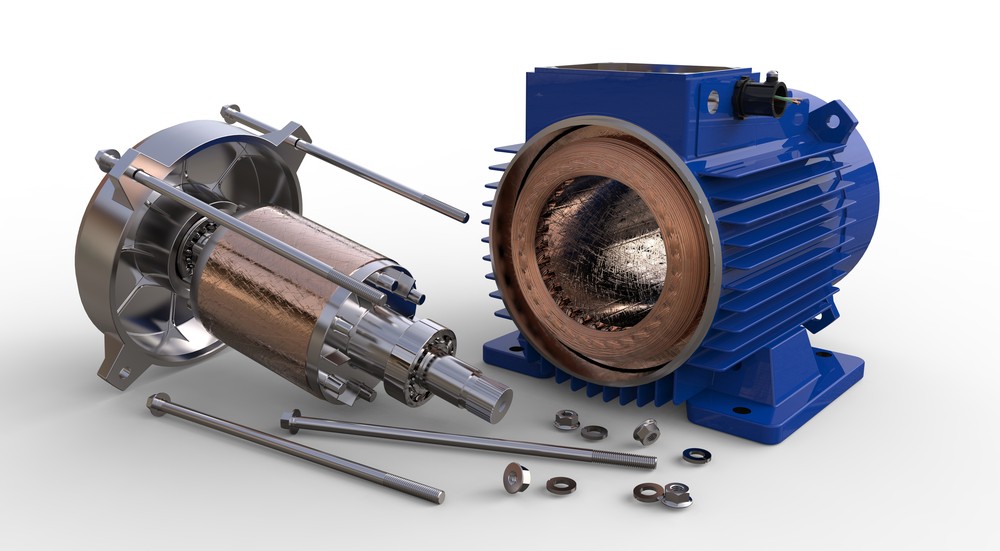
Electric motor upkeep is a cornerstone of any industrial maintenance plan. Unfortunately, even the most attentive maintenance schedule can’t prevent sporadic problems. Increasingly, manufacturers are turning to predictive maintenance models and real-time monitoring solutions for their electric motors to help improve reliability. But for many manufacturers, this isn’t an option yet. If your factory is still waiting on sensor-based solutions, there are ways to increase reliability and performance in electric motors.
How to extend the life of electric motors
Most of these tips are already part of a good routine maintenance plan. However, increasing the frequency of their administration or performing spot-checks on vital electric motors can reduce the chances of full motor failure.
- Proper lubrication. Lubrication is the single biggest factor in motor efficiency and reliability. Using the right type of lubricant with the right viscosity is imperative. Lubrication reduces heat and friction — the biggest detriments to an electric motor. Make sure the lubricant is free of any debris and that proper lubrication levels are observed to prevent contaminants or excessive bearing wear.
- Routine cleaning. Cleaning the motor is a simple task that should be part of routine upkeep. Keep the casing free of dust and debris, and make sure all venting is free of blockages. Prevent debris buildups as routinely as possible. And, make sure to clean the motor using only approved chemicals and practices so you don’t damage the casing or other vital components.
- Proper cooling and voltage control. Despite proper lubrication, heat is a problem for continuous-run electric motors. Check to make sure cooling is adequate and that venting is possible. Also, moderate voltage using an oscilloscope and make sure the motor isn’t receiving excess voltage, which can cause it to run hot and malfunction.
- Vibration tests and mounting checks. Using an ultrasound monitor, check to see that the motor isn’t vibrating excessively while in use. Some vibration is normal, but excessive vibration can affect bearing alignment and load distribution, which puts excessive wear on the motor. If vibration exceeds the bounds of normal operation, check motor mounts to ensure they’re tight and secure.
- Practice proper storage and handling. When unmounting motors — whether for service or storage — it’s crucial to handle them appropriately. Likewise, motors packed for shipment or storage should be handled with their function in mind. This includes minimizing condensation and the presence of moisture, degreasing, and planning for insulation resistance. The long-term reliability of the motor should still be top of mind, even when it’s presently out of commission.
Heat, contamination, and vibration all contribute to excessive motor wear and premature failure. These tips — along with proper routine maintenance — are key in mitigating these variables and extending the life and function of a motor. For factories not yet using sensor-based equipment maintenance plans, simply observing due diligence and best practices is the next best thing.