5 Trends Boosting Manufacturing Back to Post-Pandemic Levels
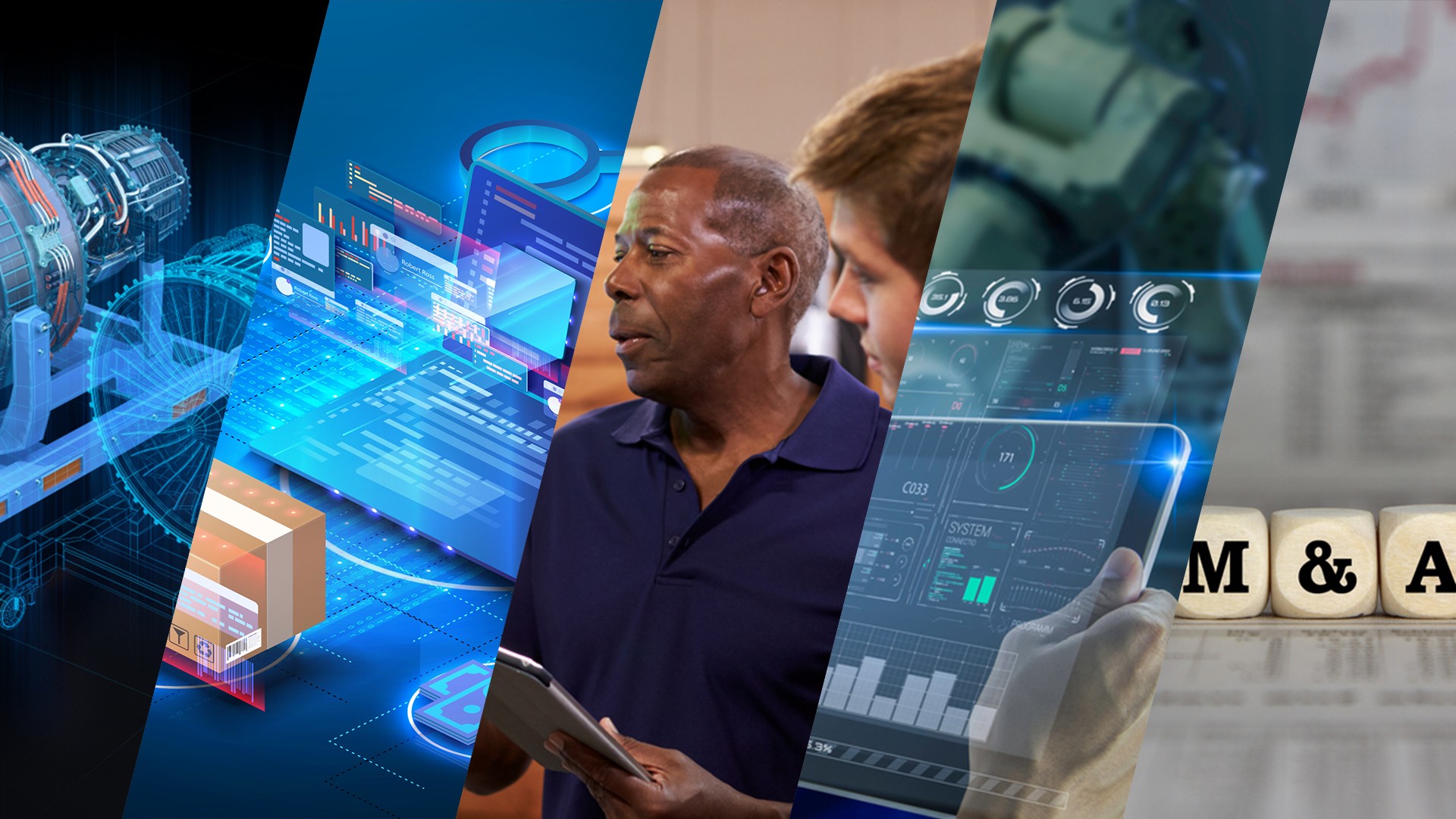
Manufacturing is stuck between a rock and a hard place in 2021. Post-pandemic recovery efforts are strong, but headwinds from the pandemic still persist. Material prices are on the rise, supply chains remain ambiguous, and supplies are backlogged. Strong demand from suppliers is putting the squeeze on producers.
Faced with difficulties on both sides of the value stream, many manufacturers are getting creative in their efforts to persevere. Here is a look at five emerging trends:
1. Digital twins and ERP
Digital twins and enterprise resource planning (ERP) software were in use before the pandemic but have found new meaning in its aftermath — namely, their ability to help manufacturers identify resources, reduce costs, and increase efficiency. Through ERP, manufacturers can get a better handle on supplies and materials, which allows them to better plan production schedules.
Through the use of real-time data collection, data twins accurately tell manufactures how to better spend their money. For example, a machine’s digital twin can show when it is due for a particular service in the upcoming month, which allows for the timely order of parts, as opposed to keeping them stocked in inventory. This lowers static costs and allows for proactive maintenance.
2. Supply chain visibility
With supply chains in disarray, manufacturers demand a greater level of transparency as they reestablish links or shift them to new suppliers. Among its many benefits, transparency allows for better end-to-end chain of custody tracking, lower shipping costs, and higher customer satisfaction.
Supply chain visibility has become much more than a manufacturer-specific problem. The shakeup of global supply chains in 2020 showed how vital it is to control the means of procurement for essential supplies. The internet of things (IoT) and machine learning offer some help in raising the standard for supply chain visibility, but many manufacturers want a complete remodel that offers them more insight and control over where, how, and when they get materials.
3. Workforce training
Manufacturing job openings are at an all-time high. Despite this, many companies struggle to find qualified employees. With demand skyrocketing, it is more important than ever for manufacturing companies to fill open positions, leading many to embrace workforce training to increase the skills of their current employees.
Companies are utilizing innovative software and webinars to upskill current employees and attract new workers who are willing to learn. Through these training programs, employees learn skills in communication, engineering, and other vital fields. The goal of workforce training is bridging the gap between unqualified workers and those willing and able to learn.
4. Digital investments
In the post-pandemic world, more and more companies are investing in digital technologies to increase efficiency. A recent Deloitte poll showed that 76% of manufacturing executives plan on making more digital investments this year to hedge against future disruption. Investments in technologies like the industrial internet of things (IIoT), data twins, machine learning, augmented reality/virtual reality (AR/VR), and more will allow manufacturers to better predict and prepare for future obstacles.
5. M&A and integrated manufacturing
Mergers and acquisitions (M&A) are common during periods of economic turbulence. Difficult economic conditions cause smaller companies to join forces or welcome acquisition by larger industry players. By merging, these companies leverage their best traits and downplay their weaknesses to grow stronger together. Now, integrated manufacturing also incentivizes smaller companies to merge to provide mutually beneficial support services.
With supply chains disrupted and other pandemic-related hardships persisting, it is more important than ever for companies to sustain operations. ERP, increased supply chain visibility, workplace training, integrated manufacturing, and digital technology investments are all solid strategies for attacking problems at both the top and bottom lines.