5 Signs of Inefficiency in Your Pneumatic Systems
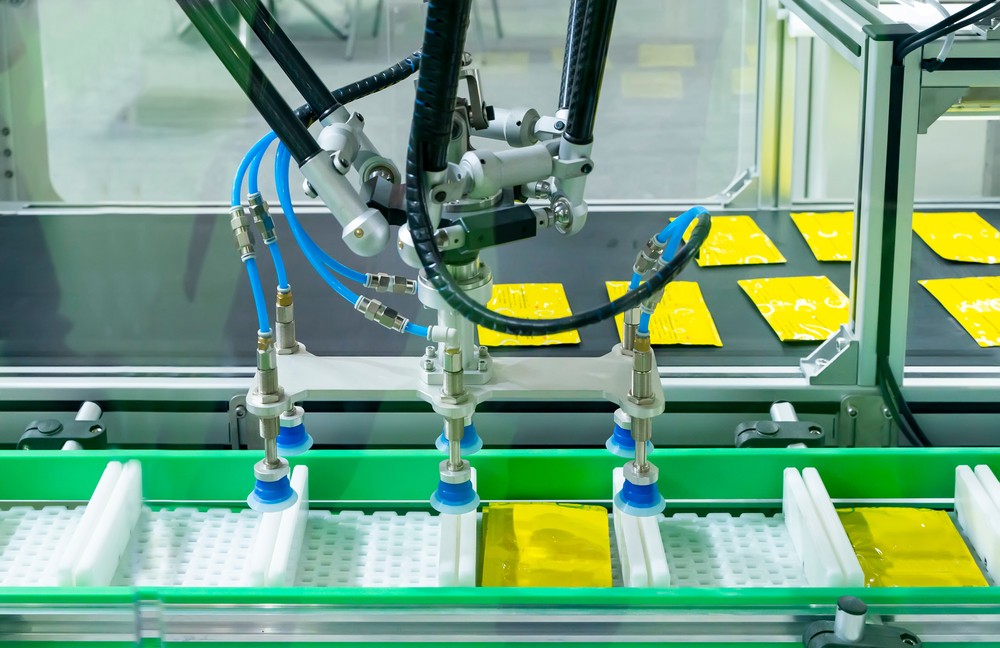
Pneumatic power systems play a fundamental role in the core operations of numerous pieces of equipment. Depending on the production environment you operate, these systems could very well govern your most critical assets. Thankfully, air power has earned a reputation for being reliable, and when given routine service and attention, pneumatic systems can outlast other types of power systems. That’s if (and only if) maintenance technicians are adept at recognizing signs of inefficiency and taking steps to remedy them before they result in failure.
Pneumatic systems can be found in factories around the world. Not only are they affordable to run and maintain, but they’re also some of the most reliable systems you can buy. Despite their penchant for longevity, there are inefficiencies that can develop if pneumatic systems aren’t properly maintained.
1. Low pressure or loss of pressure
The success of any air system rests on maintaining adequate pressure. It’s a bad sign if you’re noticing continuous low pressure or periods where the pressure drops, only to recover shortly thereafter. Service professionals should check and calibrate the compressor settings. If the issue isn’t resolved, adjustments to filters or piping may be required.
2. High operating temperatures
Is the compressor getting hot? Or is the discharge air of the compressor too hot to touch? The culprit is usually a cooling issue caused by a blocked filter, clogged cooler, or improper ventilation design. Temperature problems should be addressed immediately. A compressor that runs too hot will wear prematurely.
3. Excessive cycle frequency
One sign of compressor inefficiency is excessive cycling. As you’re monitoring your load/unload operation, pay attention to how long the compressor is in each state. Total cycle time for both states should be around two minutes at 50% loading. If you’re getting times that are too fast, reach out to your maintenance team for a repair.
4. Audible leaks
Can you hear air leaking from your compressor? If you don’t have a leak management program in place, you could be wasting up to 50% of the air your compressors are producing. Save yourself the high energy costs by working with equipment maintenance professionals to implement a leak management plan.
5. High drainage levels
One of the key indicators of an efficiency problem with your air compressor is high drainage levels. Check your condensate drains and make sure they’re removing water efficiently. How well you remove the water will impact not only the quality of compressed air, but your energy costs as well.
Keep your pneumatic power systems reliable
Like any piece of equipment in a manufacturing facility, pneumatic systems need regular attention. By staying up to date on routine maintenance, you’ll keep moisture, particles, and other problem-causing elements at bay. Partnering with manufacturing maintenance experts for routine inspections and maintenance can keep your air systems running efficiently, saving you money and keeping production on pace.