5 Future Industrial Maintenance Trends Taking Shape Today
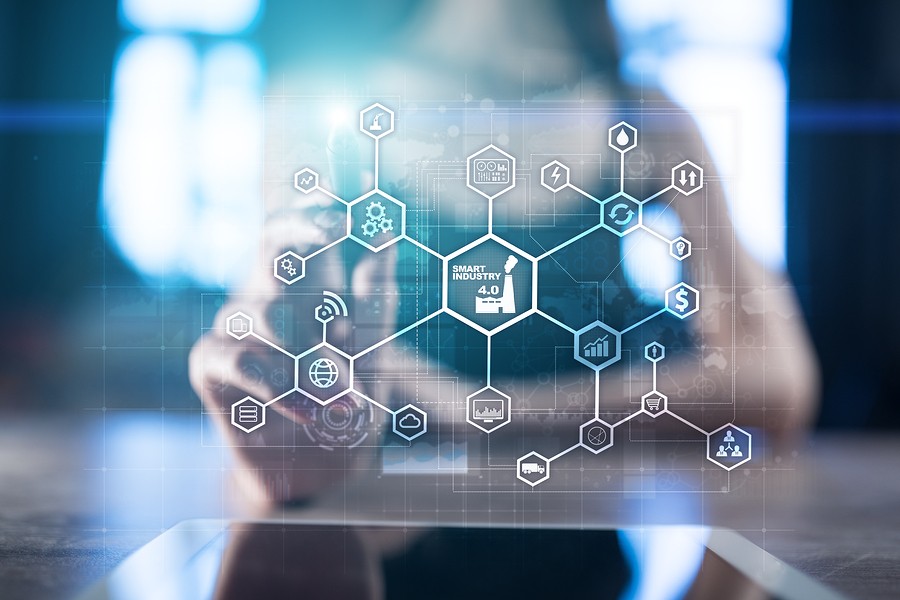
The world of manufacturing maintenance is abuzz with terms like “blockchain” and concepts like the Industrial Internet of Things (IIoT). And while these advancements are standalone subjects in their own right, they point to larger trends within the industry.
For machine owners, operators, and repair professionals, the landscape for industrial machinery is about to change. Let’s take a look at five of the biggest trends that are already taking shape:
- Subscription-based equipment maintenance — Equipment manufacturers are recognizing their ability to consolidate factory services into sales, leading to a Software as a Service (SaaS) model for industrial repair. In the near future you’ll buy or lease a new piece of machinery that comes with an enrollment plan for maintenance. That machine connects to the IIoT, sending status updates to the factory and triggering maintenance calls as needed. You’ll get the maintenance you need to keep things running while the manufacturer gets recurring business and proper oversight of the machine.
- Big data maintenance insights — Speaking of the IIoT and connectivity, big data is already profoundly changing the world of machine maintenance. Machines connected to the IIoT are subject to massive data collection through sensors and better management from maintenance professionals. Using Manufacturing Execution Systems (MES) and Supervisory Control and Data Acquisition (SCADA) systems, operators can channel data into predictive algorithms for a better approach to proactive maintenance. Likewise, real-time sensors make it easier to react to repair needs, minimizing downtime and operational costs.
- Virtual repair oversight — We’ve already talked at length about augmented reality (AR) and its potential impact on repairs. But there’s so much to be said about this exciting topic! Using computer-aided design (CAD) files already on-hand for engineering, many companies are beginning to bring AR to life through manuals with interactive illustrations. As AR becomes more prominent in the repair and maintenance space, the cost and time dedications for machine oversight will also drop.
- Decentralized repair team — Imagine an open network of repair logs, machine data, reference documents, and employee training materials. Your in-house repair team will have access to all of this anywhere in the world via the cloud, allowing them to perform the right repairs, at the right time, regardless of which facility they’re located at. For companies with a global presence, this represents significant optimization of their workforce and maintenance expenses. Instead of in-house staff at every site, your repair team can brief themselves on repairs in San Francisco and perform them in Dubai tomorrow. No more outsourcing with variable results and costs, either!
- Additive manufacturing in maintenance — This is the boldest concept in the future of industrial maintenance, yet one with the largest potential for efficiency. Imagine having a factory repair tech come to your facilities, diagnose a repair, and print the replacement part needed right then and there. As additive manufacturing becomes more innovative, this solution becomes more viable. This would eliminate replacement part ordering and dramatically reduce repair times, bringing manufacturers closer to a zero downtime endgame.
While some of these trends may seem more far-fetched than others, it’s reasonable to assume we may see them implemented in the near future. Whether that future is five or 50 years away is still unknown!
Regardless of what trends come to light, you can count on the professionals at Global Electronic Services for all your industrial electronic, servo motor, AC and DC motor, hydraulic, and pneumatic needs — and don’t forget to like and follow us on Facebook!