3 Money-Saving Reasons to Outsource Maintenance Repairs in 2020
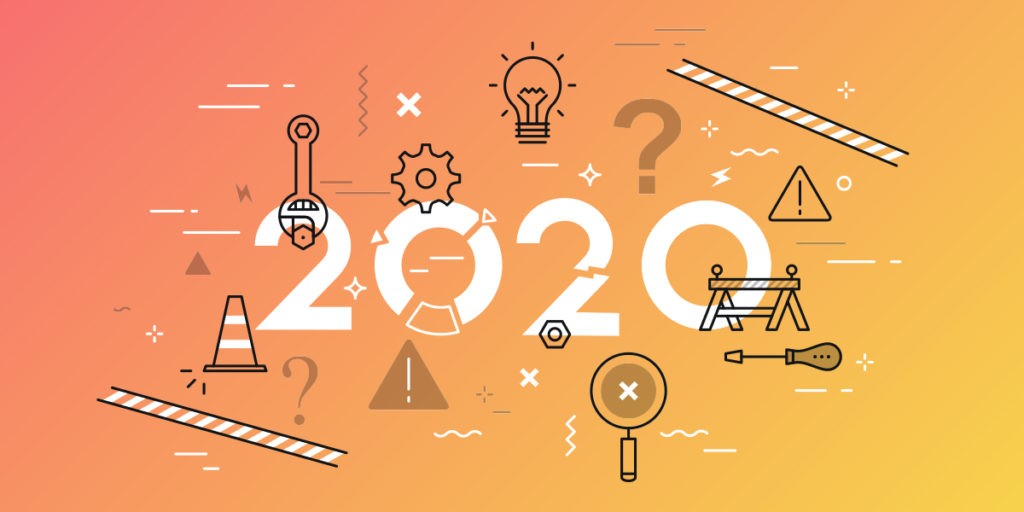
Machine maintenance and repair are central to plant operations. As such, they demand the most oversight in terms of scheduling and planning. But sometimes, the best way to gain more control over these essential standards is to observe less control over them. We’re talking about outsourcing! It’s a hot topic among manufacturers both for and against, but there’s no denying the cost benefits and savings that come with it.
Outsourcing can be a touchy subject for some manufacturers. It’s hard to trust vital repair and manufacturing to someone you can’t directly supervise or who doesn’t fall under your administrative umbrella. But for manufacturers willing to step back and look at the cost of outsourcing, there are some undeniable opportunities.
Quick service response, for less downtime
For complex repairs and maintenance, logistics are a big factor. Ordering specialty parts, scheduling the right technicians, and getting manufacturer input all take time, and time is money. For every hour that machine isn’t running, you’re accumulating negative costs.
When outsourcing, experience is a function of service, which means it’s in the best interest of your partner service provider to act fast. Moreover, they’ll have the parts and training available to remove logistical barriers. It’s very likely the price you pay for outsourced service will be less than the combined costs associated with in-house repair.
Keep in mind, even if you do keep your staff up to date on training and stock inventory parts, these are spent costs that also factored into the repair.
Reductions in capital expenditures
There are significant capital expenses tied up in having in-house maintenance and repair services. From inventorying parts, to using a computerized maintenance management system (CMMS), to purchasing specialized tools and equipment, these costs are ongoing and cumulative. Outside of personnel, capital expenses for maintenance and repair is unmatched, making it a huge cost center for any business.
In outsourcing maintenance, that cost center suddenly becomes nominal. As contractors and partner service providers assume repair and maintenance responsibilities, the cost burdens associated with them shift away from manufacturers. This is a fundamental way to ramp down maintenance, repair, and operations (MRO) costs without losing scalability.
Reduction in staffing and training costs
Think about the cost of every salary included in your maintenance department. Now, factor in ongoing training costs for these individuals. Specialized training certifications? Employee costs can quickly add up. If cost control or mitigation is a key focus, tamping down in-house maintenance may start with consolidating staff.
The costs saved outsourcing won’t likely ever come close to offsetting those charged by on-demand MRO services. Scaling down the maintenance department via outsourcing repairs can unburden manufacturers in a way that allows them to do more with their MRO approach, such as investing in a preventive maintenance strategy or more heavily in the Industrial Internet of Things (IIoT).
Outsourcing repairs cuts costs
The best way to capitalize on outsourcing is through a reliable partnership with a proven service provider. Not only can the right partnership mitigate costs, it can prevent future costs from arising via quality of work.
Outsourcing may be a divisive concept for manufacturers, but there’s no denying the cost-saving benefits it unlocks.