3 Common Lubrication Problems That Are Sometimes Missed
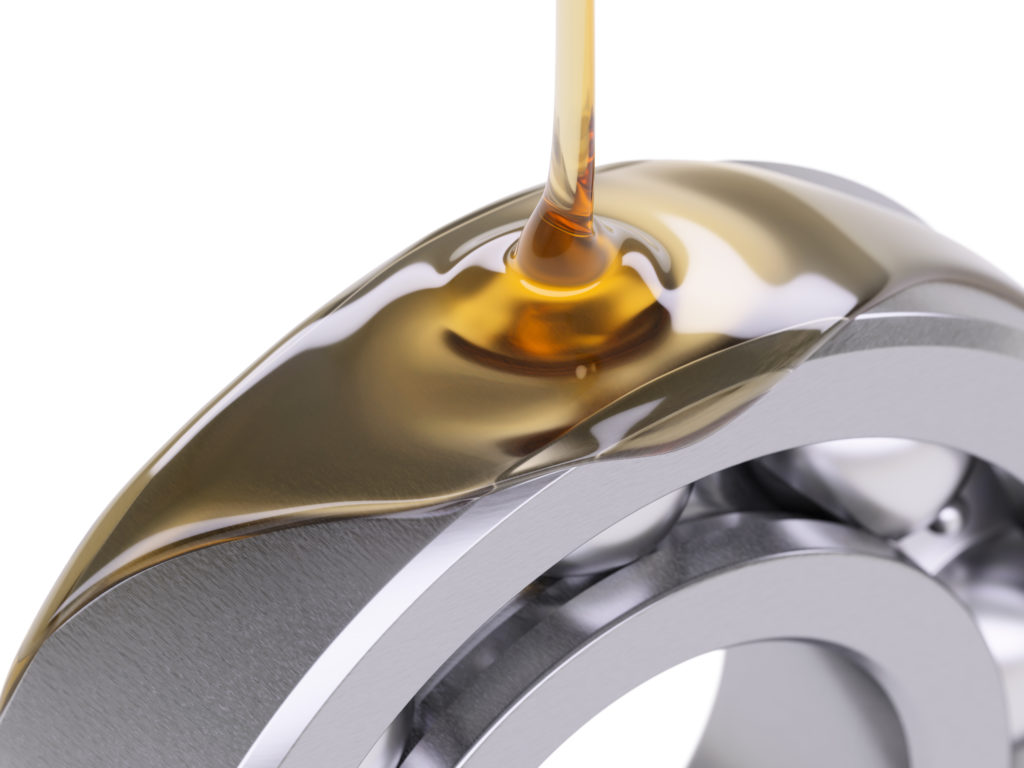
It is no secret that one of the cornerstones to a successful preventative maintenance program is good practices when it comes to lubricating mechanical equipment. Any device that has the potential for metal on metal contact is one that can suffer a high rate of failure if not properly maintained. Every maintenance worker we have ever spoke to has his own opinion on what constitutes a proper lubrication procedure. It is one of those subjects that when it comes up – everyone’s an expert. But there is a few things we see guys in the field do – or not do – that can cause some serious issues. Here are some tips to help avoid some potential problems when lubricating your equipment.
What is the first thing you check?
What is the first thing you do when walking up to a bearing that needs a little grease? Do you do an inspection of the bearing? Do you read up on the manufacturers guidelines on what type of grease to use for that motor? Do you check the schedule to see when is the last time it was greased? These are all good practices but the one thing we ALWAYS see folks forget is to inspect the grease gun itself! Especially the tip. The reason this is important is that the end of the gun where the grease comes out attracts particles of dirt, metal and other contaminants. Often the gun is stored in a not so clean environment. If you don’t clean the gun before use, you are just pushing this stuff straight into the bearing which will lead to premature failure.
Are you over greasing?
This is a big one. Greasing a bearing or any moving mechanical apparatus is one that should follow manufacturers guild lines. This all comes down to organization and proper documentation. If a maintenance crew is only reactive – meaning they only lube their equipment in reaction to a failure elsewhere in the plant – they are most assuredly over lubing something, somewhere. What over lubing causes is that the grease inside will become so thick the balls will no longer roll, but slide around. When this happens, the grease gets whipped up and the base oil within the grease will begin to separate from what is called the “soap” of the grease. This will cause the grease to lose its lubricate properties and lead to a premature failure of the bearing.
Are you checking what type of lubrication is appropriate?
One of the easiest traps to fall into is keeping only one type of grease on hand for your personnel to use to lubricate all your equipment. There is a lot that goes into choosing a type of grease that should be used for any applications. Grease consistency, thickener type, base oil makeup, additives – these things relate to what type of grease you are buying and what type of bearing it is appropriate for. While all the choices on the market can be daunting, the fastest and easiest way to both know what to keep on hand, in addition to making sure your guys are using the right stuff is to read your machines literature! Very rarely does a machine not include some sort of guide to lubricating the mechanical.
Remember, the best way to keep your mechanical side running is to properly lubricate the machine! But if you do find yourself in a failure situation you can always call us! Be sure to visit us online at gesrepair.com or call us at 1-877-249-1701 to learn more about our services. We’re proud to offer Surplus, Complete Repair and Maintenance on all types of Industrial Electronics, Servo Motors, AC and DC Motors, Hydraulics and Pneumatics. Please subscribe to our YouTube page and Like Us on Facebook! Thank you!